-
Publications
-
Research activities
-
Hybrid mobile hydraulics for excavators
-
Lubricating Systems with Rotating Shafts
-
0D models of axial piston pumps/motors
-
CFD studies on conical poppet valves
-
CFD analysis of gerotor pumps
-
Lumped parameter models of crescent pumps
-
Lumped parameter models of vane pumps
-
Lumped parameter models of gerotor pumps
-
Coupled simulation of telehandler hydraulics
-
Modelling of brake booster vacuum pumps
-
Absorbed energy in ICE lubricating pumps
-
Multi-body simulation of axial piston pumps
-
Development of variable flow lubricating pumps
-
Optimization of ICE lubrication gerotor pumps
-
-
Research projects
Lumped parameter models of vane pumps (2001-2004, 2012-2017)
Very detailed 0D models of low and high pressure variable displacement vane pumps have been developed starting from 2001 in Simcenter Amesim. The geometric quantities are calculated analytically starting from the main parameters of the pump as function of the shaft angle and of the stator eccentricity. Different leakage paths are considered and the axial clearances are variable in order to take into account the deformation of the pump cover. The vane tip clearances are calculated as function of the dynamic equilibrium equation of the vanes and the specific shape of the vane tip is taken into account for the calculation of the leakage flow. The displacement control considers the internal forces on the stator due to the pressure in all variable chambers and to the contact force exerted by the vanes. Both stators with linear and rotary motion can be simulated and the influence on the effective eccentricity and on the pump timing due to the movement of the stator centre along the X and Y axes are considered. The model can exploit different oil aeration models implemented in the Simcenter Amesim.
In figure 1 the model of a lubricating pump with absolute pressure limiter is shown. Some of the customized components are the following:
- calculates the pressure for all variable chambers,
- calculate inlet and outlet flow rates,
- calculates the inter-chambers leakages
- calculates the axial leakages
- simulates the stator dynamics,
- calculates the volumes and derivatives of the chambers,
- calculates the flow areas,
- supplies the geometric parameters
Figure 1
In figure 2 the delivery pressure is plotted with two different separated air fractions measured using the X-ray technique.
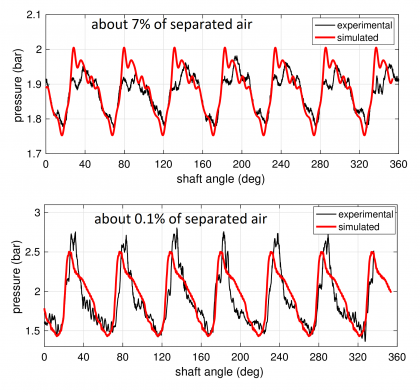
In figure 3 the capability of the model to simulate the axial gap compensation in a high-pressure industrial pump is reported. In the pump under study the deformation of the port plates due to the pressure was able to decrease the axial clearances, leading to an improvement of the delivery flow rate with respect to the case with constant gaps.
Figure 3
In figure 4 the delivery pressure and the stator eccentricity during a transient with a sudden increment and reduction of the load is shown: the displacement control reacts accordingly in order to limit the delivery pressure at the mean value of 210 bar.
Figure 4
More analyses and details are available in: